No rust, just metal fatigue. Got pics. I should have taken a wider angle view for more perspective.
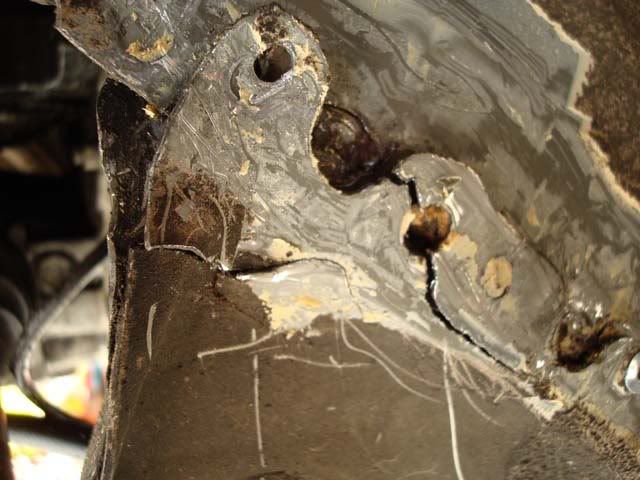
This is top or forward part of where the control arm box attaches to the frame.
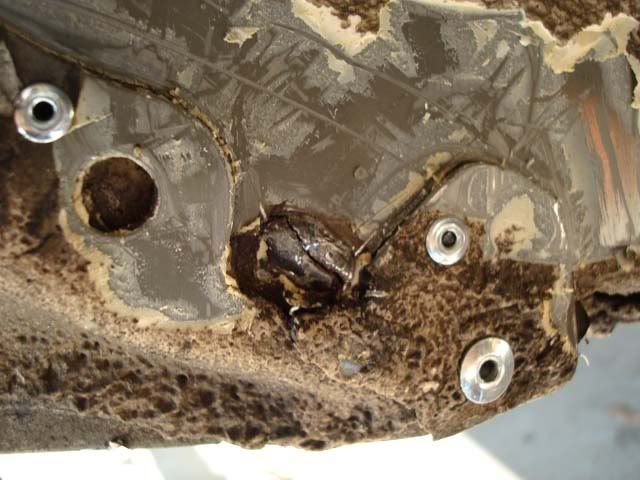
This is the box near the bottom. Note that it looks like it may have been welded here before. The weld is cracked. The cracked weld would have been done at the factory as it had the factory coating over it.
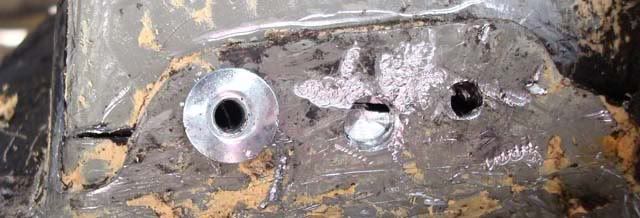
This is the front of the control arm box looking straight up. The frame is also cracked, you can see the crack through the hole I started to drill for a pop rivet. BTW the pop rivets are just to make it safe enough to drive to the shop.
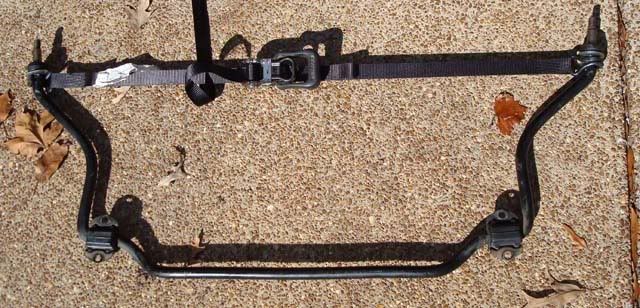
For those who have changed your sway bar bushings, is that sway bar supposed to be about 4" wider that the spacing of the holes in the control arms? I had to squeeze it in. How do you like this trick, used a cargo strap with a turn buckle. I balanced the bar on the floor jack while I put it in place and bolted it down.
My friend with the body shop ran out of welding wire. I went to a local small engine shop that does welding and he is willing to do it, but can't get to it till Thursday at the earliest, but I can't get back till Saturday. I talked to my friend tonight, he has the weld wire now and he tells me he's done a lot of repairs like this. Says he'll make a doubler plate as well.
I was going to make a doubler plate a t work from 10 ga but he tells me that this is too thick, has to be the same as the original metal which looks to be 16 or 18 ga. I think maybe he just can't cut or bend 10 ga, but I can. We have a 400 ton press brake at work. We have one larger but I've never operated that one.
Anyway, not sure which way to go, experienced or amateur where I have more control.